The Problem
Brinell hardness measurement is a rough measure of the material properties of a sample. It involves using a hard ball to indent the material being tested, and then measuring the size of the indentation. The larger the indentation, the softer the material is since the ball was able to penetrate deeper. Sounds pretty simple, right?
This process actually has many variables that can affect the end result.
The indentation can be performed using several different tools including a stationary air-driven press or a hand-pumped device that is clamped onto the item being tested.
When reading the indentation, many different methods can be used. The cheapest method uses a handheld microscope-like device with two vertical lines. The user lines up one of these lines with the edge of the indentation and then twists a knob to bring the other line to the opposite side. By reading the amount incremented by the knob, the diameter of the punch can be measured. From there, the associated hardness reading is looked up from a table. Obviously this method includes a lot of human factors such as vision, motion accuracy, and correctly interpreting the result.
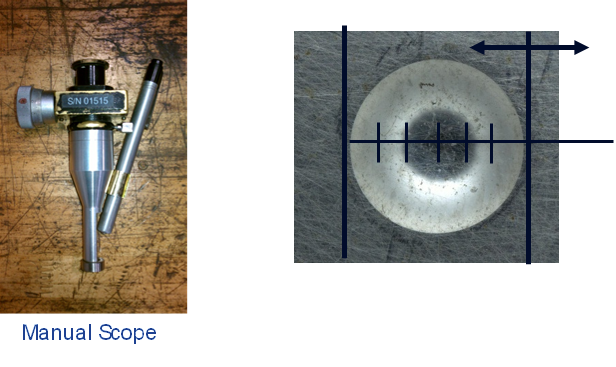
In contrast, there are automated systems available which will capture an image of the indentation and calculate the hardness reading with minimal human influence.
Before indenting a surface, it must be smoothed using a grinder. This can be either a sand or stone based grinding wheel, and the grinding force applied can vary between inspectors performing the operation. This can work-harden the surface, and this effect depends on the original hardness of the material.
Our task was to determine how some of these variables affect the final hardness reading and propose solutions where needed.
Hardness Reading
The main focus of the project was the reading of the hardness punch. Different manufacturing cells used different methods of measuring the indentation diameter, so we wanted to see what kinds of errors resulted from each method. We devised a double-blind gage R&R test that had the inspectors check pre-punched samples using three methods of measurement: the manual scope and two competing automated systems.
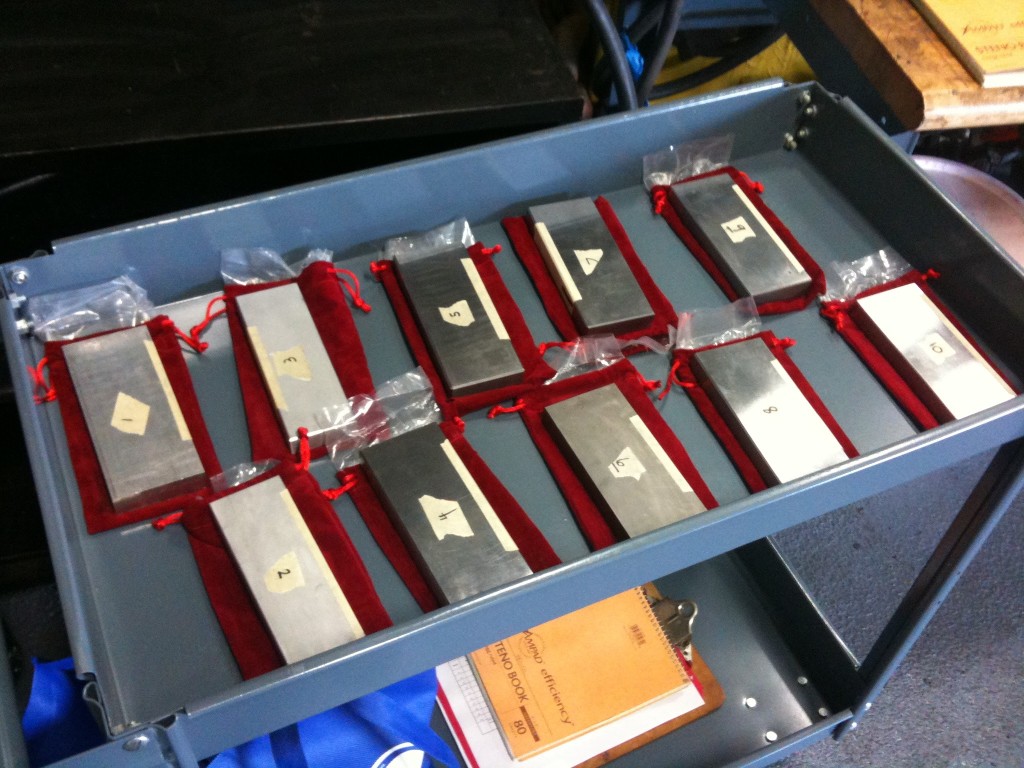
To obtain known hardness values, we used calibration blocks straight from the manufacturer. These blocks had 5 punches already made with hardness values disclosed for each. We covered up the hardness values, randomly assigned a number to each block, and then randomized the order in which the blocks would be handed to the inspectors. The inspectors would then test each punch and announce the result, which we would record. Each block was tested at least 3 times by each inspector with each punch measuring method.
Once all the data was gathered, we were able to remove the masking tape from each block, revealing its true hardness. We then compared the readings from the inspectors to the known values to compute the error in hardness reading using statistical analysis methods such as ANOVA.
Grinding
Another variable in the process is the way in which the surface is prepared. The two main kinds of grinding media are sand or stone, so these are the two that we tested. However, the user can exert any amount of force, which could potentially work harden the surface and skew the result.
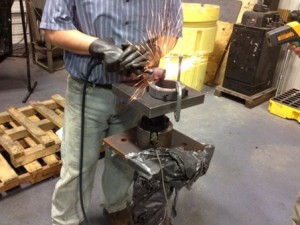
Thus, we devised a test fixture that would measure the load applied by the grinder using a load cell. I set up a simple data acquisition system using National Instruments hardware and LabVIEW, and we had the inspector grind softly, with moderate force, and with great force on various samples. We correlated the load applied to the resulting hardness reading to determine the effect (if any) of grinding force and media.
Heat Treating
Another factor that applies to work hardening the surface is the initial strength of the material. To test this, we got to use an industrial furnace to heat treat samples to achieve material properties ranging from very soft to very hard.
These samples were used in the grinding experiment to see how much the hardness could be changed by the grinding process based on the initial hardness of the material.
Conclusion
While I cannot disclose the results of the study (it’s GE proprietary information), I can say that I learned a lot about material properties and hardness testing from this project. I was able to use many aspects of engineering to come up with experiments to test various aspects of the hardness testing process, and I got to interface with inspectors, cell leaders, shop floor managers, master black belts, material scientists, and even the vice president of engineering.
I was pleased to receive the following feedback from my manager:
“Thank you for the work you did on your Green Belt project. Your ability to work with various functions and groups enabled you to gather valuable data that led to critical changes to improve the hardness reading process. The experience and knowledge you gained during this process will benefit you as you grow in your career. Thank you for putting forth a tremendous effort!”